Laser beam welding is a highly sophisticated and automated process that offers several benefits over conventional welding techniques. This advanced joining process offers superior precision, speed, and efficiency, making it an ideal choice for a variety of industrial applications. However, laser beam welding also requires strict adherence to safety measures and process control. In this article, we’ll discuss some of the key aspects of laser welding and how to ensure its safety and efficiency.
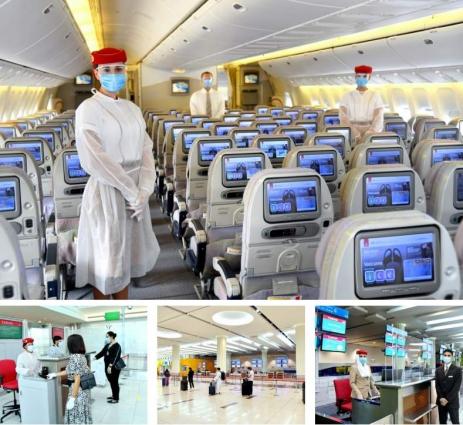
What is laser beam welding?
Laser beam welding is a process that involves the use of high-intensity lasers to join two or more pieces of metal. The laser beam generates a concentrated and intense heat source that melts and fuses the metal parts together. This welding technique offers several advantages over traditional welding methods, such as TIG or MIG welding, including:
- Better precision and accuracy
- Higher welding speed
- Lower heat input and distortion
- Reduced use of filler materials
As a result, laser beam welding is widely used in various industries, such as aerospace, automotive, medical, and electronics.
Process control for laser welding
Laser beam welding is an automated process that requires precise control over various factors, such as laser power, focus, positioning, and speed. These parameters can affect the quality, strength, and durability of the weld joint. Therefore, it’s crucial to monitor and adjust these parameters throughout the welding process to ensure consistent and optimal results. Some key aspects of process control for laser welding include:
- Laser power: The laser beam’s power determines the amount of energy that is delivered to the workpiece. The power must be adjusted based on the material thickness, welding speed, and joint design. Too little power can result in incomplete melting, while too much power can cause excessive heat input and distortion.
- Focus: The laser beam must be focused on the workpiece to generate a narrow and intense heat source. The focus position and spot size must be optimized based on the material properties and joint geometry. A misaligned or unfocused laser can result in a weak or irregular weld.
- Positioning and speed: The movement of the laser beam and the workpiece must be synchronized to ensure a consistent and smooth weld. The speed and direction of the motion must be adjusted based on the joint design, welding position, and accessibility. Too slow or too fast movement can compromise the weld quality and integrity.
Safety measures for laser welding
Laser beam welding involves the use of high-intensity lasers that can pose significant risks to the operators and bystanders. Therefore, it’s essential to implement strict safety measures and provide adequate personal protective equipment (PPE) to ensure everyone’s safety. Some key safety measures for laser welding include:
- Eye protection: The laser beam emits intense light that can cause severe eye damage or blindness. All workers in the welding area must wear appropriate protective eyewear, such as laser safety glasses or goggles, that can block the specific wavelength of the laser used.
- Skin protection: The laser beam can also cause burns or skin damage upon contact. Workers should wear protective clothing, such as flame-resistant jackets, gloves, and boots, to prevent exposure to the laser beam or hot materials.
- Ventilation: Laser welding produces fumes and gases that can be harmful to inhale. Proper ventilation systems, such as exhaust fans or hoods, must be installed to remove the fumes and maintain a safe working environment.
- Training and supervision: Workers must receive adequate training and supervision on laser welding techniques, safety protocols, and emergency procedures. Supervisors must monitor the work area and ensure that all workers are wearing appropriate PPE and following the guidelines.
Conclusion
Laser beam welding is an advanced and efficient joining process that offers various benefits over traditional welding methods. However, it requires strict adherence to process control and safety measures to ensure it’s safe and effective. By following the guidelines and providing adequate training and supervision, laser welding can be an excellent solution for various industrial applications. As a leading provider of laser welding solutions, XQL has extensive experience and expertise in delivering top-quality results while maintaining a safe working environment. Contact us today to learn more about our services and capabilities.