When welding carbon steel and low alloy steel, some important things to know include:
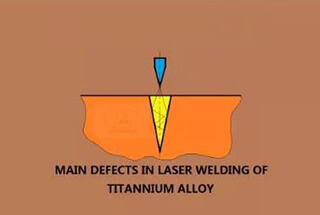
1. Carbon Equivalent
When the carbon equivalent exceeds 0.3%, the welding process will become more difficult. This is because high levels of carbon generate heat during welding, which results in the material becoming brittle. As a result, welding becomes more difficult, and the material is softer and more ductile.
2. Cold Crack Sensitivity
The cold crack sensitivity of carbon and low alloy steel is a challenge, particularly when welding thicker pieces. As the thickness increases, the weld is exposed to a greater amount of heat, which can cause warping, shrinking, and cracking. To overcome this challenge, welders use the correct welding technique or ‘welding pattern’ to prevent warping.
3. Brittle Fracture Tendency
When carbon and low alloy steel undergoes welding, the material's tensile strength or ‘yield strength’ decreases, making it more prone to brittle fracture. This can be eliminated by conducting a non-destructive test to check for cracks or fissures within the material before starting the welding process. Welders should also select a welding wire that has a higher toughness to prevent brittle fracture.
In conclusion, laser welding is an excellent choice for welding carbon steel and low alloy steel. However, to ensure a successful welding process, welders must take the above factors into account. By following proper welding techniques and selecting the correct welding wire, laser welding plants can achieve precise, high-quality results.