Fuel injectors are a vital component of a vehicle's engine system. They are responsible for delivering fuel into the combustion chamber in a precise manner, ensuring that the engine runs smoothly and efficiently. As such, it is crucial for fuel injectors to be designed with the highest level of precision and accuracy and fabricated using top-quality materials.
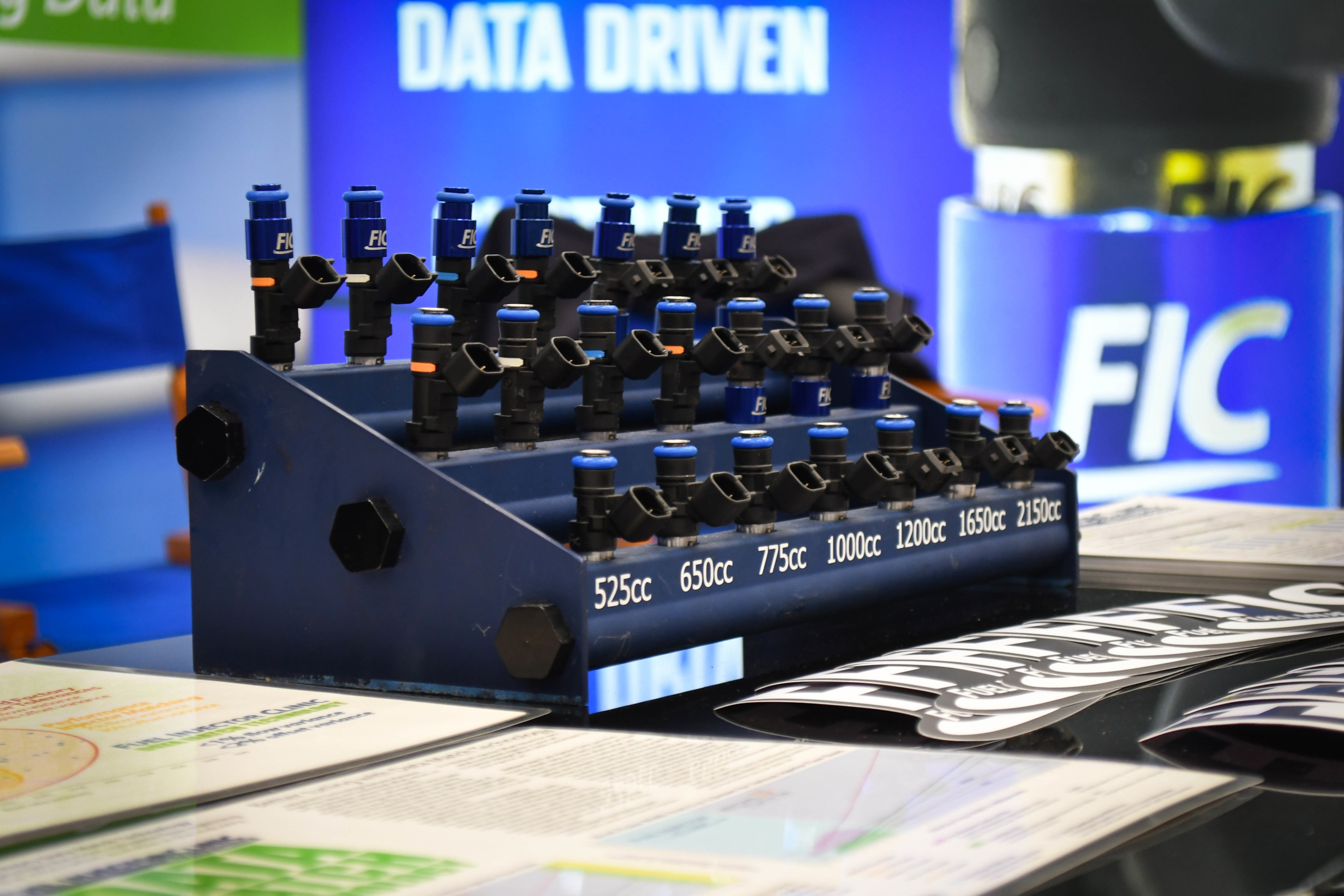
One of the most important processes involved in the manufacture of fuel injectors is precision welding, which is widely regarded as a critical step in producing high-quality, high-performing injectors.
Precision welding is a method of welding that utilizes advanced technologies and techniques to fuse metals in a highly precise and controlled manner. The process involves the use of a high-energy beam or electrical arc to melt the metal surfaces to be welded, creating a bond between the two parts.
Precision welding has many benefits that make it ideal for fuel injector applications. For one, it allows welders to precisely control the amount of heat and energy being applied to the metal surfaces, which helps prevent warping, cracking, and other defects that can affect the performance of the injector. Additionally, precision welding can be used to join dissimilar metals or thin materials, which can be difficult to do using other welding methods.
When it comes to fuel injector development, precision welding plays a critical role in ensuring that the injectors meet high-performance standards. Fuel injectors that have been precisely welded are more likely to perform optimally under a wide range of operating conditions, providing drivers with better fuel economy, increased power, and smoother engine operation.
Precision welding is not the only aspect of fuel injector development that is essential for achieving high-performance results. Other factors, such as design and fabrication, also play a significant role in determining the effectiveness of fuel injectors.
Design and Fabrication of Fuel Injectors
Designing and fabricating fuel injectors involves the use of advanced computer-aided design (CAD) software and other modeling tools to create a prototype that can be tested and refined until it meets the necessary performance requirements.
During the fabrication process, precision machining is used to create the various parts of the injector, which are then assembled and tested for quality and performance. Once the injector has been fully assembled and tested, it is ready for installation into the engine.
Forced Induction Systems
Forced induction systems are another critical component of high-performance engines. These systems work by increasing the amount of air that is flowing into the engine, which in turn increases the amount of power that can be produced.
Precision welding plays a crucial role in the development of forced induction systems, as it allows designers and fabricators to create complex components that are finely tuned to the specific needs of each engine. This level of precision is essential for ensuring that forced induction systems provide the maximum level of performance and reliability.
In Conclusion
Precision welding is a vital component of fuel injector development and is essential for achieving high-performance results. Alongside design, fabrication, and forced induction systems, precision welding ensures that fuel injectors provide drivers with optimal fuel economy, power, and engine operation.
If you're in the market for high-performance fuel injectors, look for manufacturers that use precision welding and other advanced manufacturing techniques to produce superior quality injectors. By choosing a manufacturer who prioritizes precision and quality, you can be confident that your engine will perform at its best.