Plastic and composite materials are widely used for various applications in industries such as automotive, medical, electronics, and aerospace. However, joining plastic components has always been a challenge due to the material's low melting point and difficulty in bonding with traditional methods. Fortunately, advancements in laser technology have brought about a new process for plastic joining – laser welding of polymers.
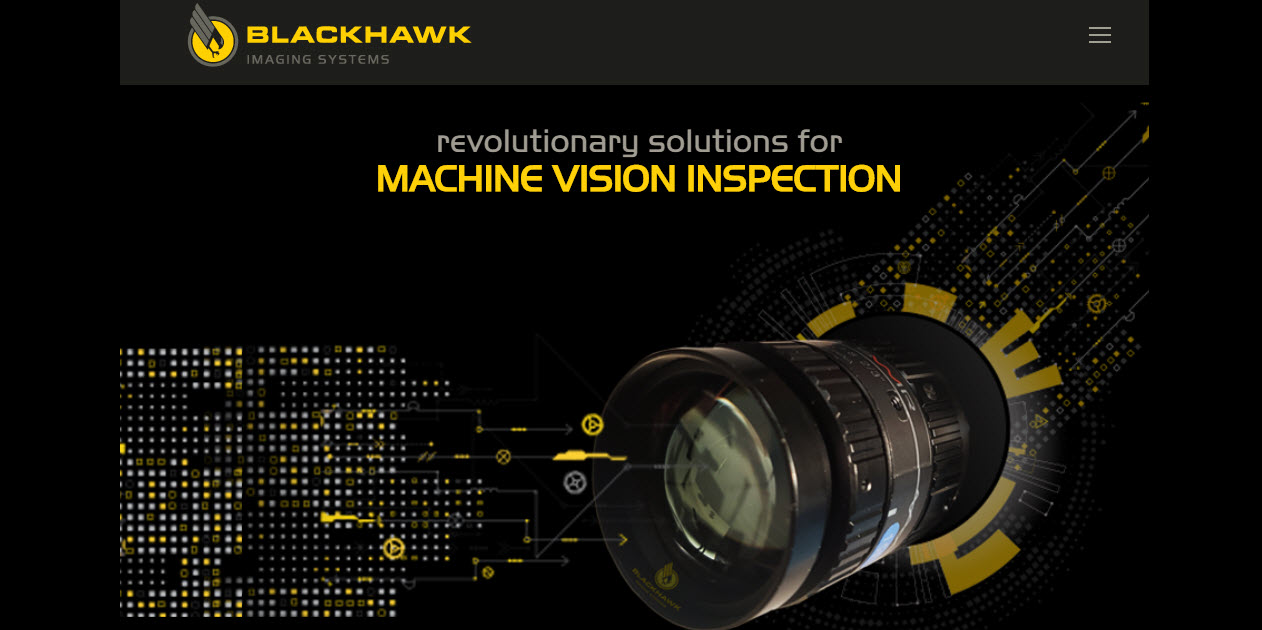
What is Laser Welding of Polymers?
Laser welding of polymers is a process that uses laser energy to join two plastic or composite components without additives or adhesives. The process is a contactless and non-contact welding process where laser energy is directed to the joint to melt and fuse the polymer components, creating a strong and durable bond. The laser welding process is highly precise and requires minimal heat input, which prevents distortion or damage to the polymer components.
How Does Laser Welding of Polymers Work?
The laser welding process starts with the alignment of the plastic or composite components to be joined. A laser beam is directed to the joint, and the energy from the laser heats the material's surface rapidly, causing it to melt and fuse together. The melted surface cools and solidifies immediately, creating a robust bond.
Advantages of Laser Welding of Polymers
Laser welding of polymers offers several advantages over traditional welding methods. These advantages include:
1. Strong Bonds: The laser welding method creates strong and durable bonds without the need for additives or adhesives, which ensures the integrity of the joint.
2. Suitable Material Selection: Laser welding of polymers can be used with a great variety of plastics and composites, providing more flexibility in material selection.
3. Precision: The laser welding process is highly precise and can be used to create intricate designs or join complex shapes.
4. Time-Efficient: The process is more time-efficient than traditional welding methods due to its high speed and single-step process.
5. Environmentally Friendly: The laser welding method is eco-friendly as it does not require additional adhesives or additives and produces minimal waste.
6. Cost-Effective: While the initial investment in a laser welding machine is high, the long-term cost-effectiveness of the process outweighs traditional welding methods' cost.
Pes Laser Welder Cost
The cost of a PES laser welder depends on several factors, such as the machine's quality and features and the application requirements. However, investing in a PES laser welder is a wise decision as the process can provide long-term cost savings and increased efficiency.
Conclusion
Laser welding of polymers is a revolutionary process that provides strong, durable, and environmentally friendly bondings. The process's precision, time efficiency, and flexibility in material selection make it ideal for various industries that require joining plastic components regularly. Moreover, despite the initial investment's cost, investing in laser welding equipment can provide long-term cost savings and increased efficiency, making it a wise decision for any business that requires plastic welding.
In conclusion, laser welding of polymers is a game-changing process that has opened up a new world of possibilities in plastic joining. The process's advantages, including strong bonds, cost efficiency, environmentally friendly production, and precision, make it an ideal solution for a wide range of industries. Businesses can invest in the best PES laser welder cost to ensure long-term success and higher efficiency.