Description
Jinggong robot integrates many years of experience in the logistics industry and has developed a logistics system software system basic business platform and development platform with independent intellectual property rights, integrating standardized design and personalized customization development. The application system model is constructed by using workflow mode. Follow the concept of modern logistics, put forward comprehensive and complete system solutions, and realize the perfect unity of automatic storage and automatic production logistics. Basic parameter configuration: define, configure and manage parametric settings, complete user role permission definition, application system function configuration, storage location configuration, logistics path configuration and business process configuration, and realize the application of customer localization. Adopt the customer standard coding architecture, establish and maintain unified coding management, and provide basic information guarantee for the unified management of each library; task management Manage the goods in / out business and handling process, support batch management and material tracking, including normal business process processing, exception process processing and emergency task processing. Graphical interfaces such as material access path tracking and alarm. Adopt graphical inventory management technology The information of inventory, location and storage area shall be managed intuitively and graphically, and the inventory situation and the situation in the warehouse shall be displayed in real time. Statistical query Support customer-defined statistical query, including daily, monthly and annual statistical reports. Data excel text import and export. Intelligent interface system The interface program is constructed by defining a unified interface and common standard components independent of hardware platform, operating system and programming language. Xinsong logistics information management system can maintain independent operation mode, and can also be seamlessly integrated with underlying equipment and related software systems. The superior system can be used as the command center to deconstruct and assimilate its various businesses and data into the internal instructions and data definitions of Xinsong logistics system. data acquisition system RFID is the abbreviation of radio frequency identification, namely radio frequency identification technology, one-dimensional and two-dimensional bar code technology. Independently designed and developed data acquisition system platform software, developed RFID group reading middleware, bar code group reading technology and middleware, integrated various information acquisition equipment, unified and scientific coding of handling containers and man-machine operation platforms, fast and accurate positioning, fast and efficient data acquisition and information processing, which can not only track the path of a single material container, but also manage the whole process of material items, Realize agile data collection and material management. Monitoring and dispatching system Independent research and development of special configuration software for logistics, using OPC Technology for process control, as an industrial standard interface. Realize the graphical management of equipment, integrate the video monitoring system, monitor the overall operation in real time, dynamically display the operation status, location and fault alarm of equipment, provide manual intervention function, and develop the alarm business of mobile terminal. Realize management task decomposition and path optimization, send it to the equipment control system through PROFINET Industrial Ethernet, and feed back to the logistics management system after receiving the completion or alarm information of the control equipment. Wireless terminal and forklift navigation system The handheld mobile system and forklift navigation system developed by wireless network technology realize the online process management of manual handling. Realize the wireless collection and whole process tracking of material information. The design of operation interface is simple and clear, and the operation is convenient. Effectively manage the connection of wireless network terminals to improve the security of the system. Automated production logistics system Based on the traditional automatic warehouse management, realize the control and management of the automatic production line, meet the material handling of each production area through high process configuration, and make the automatic warehouse highly integrated with the automatic production line. It has the functions of process flow management, production set, production material preparation, production scheduling, production distribution path planning, production assembly guidance and so on. It is integrated with MES system to reduce manual intervention process. It is widely used in discrete manufacturing industries such as assembly inspection to build an automatic digital workshop. system simulation Jinggong robot applies the latest and most authoritative simulation software in the logistics industry: AutoMod (version: 12.3.1) of American applied materials company to simulate the virtual construction and production of the logistics system scheme, and carries out the simulation operation according to the data provided by the customer to test the rationality of the system process in the project. For pick-up and delivery equipment, the capacity simulation calculation of single equipment is adopted. Within the set simulation time range, each receiving and delivery process applies for the delivery task according to the actual flow, and the equipment processes the receiving and delivery according to the order of the application queue. The calculation principle is to track the running track of the equipment, count the running times of the equipment operation, combine the calculation formula of the one-way operation time of the equipment, and consider the receiving and delivery time, communication and other auxiliary time to calculate the processing capacity of the equipment. Through the whole logistics analysis and application of the simulation model of AutoMod system simulation software, the operation process of the production process of the automatic storage system is simulated, which can explain whether the logistics planning and design can meet the use requirements.Product Video
Product Show
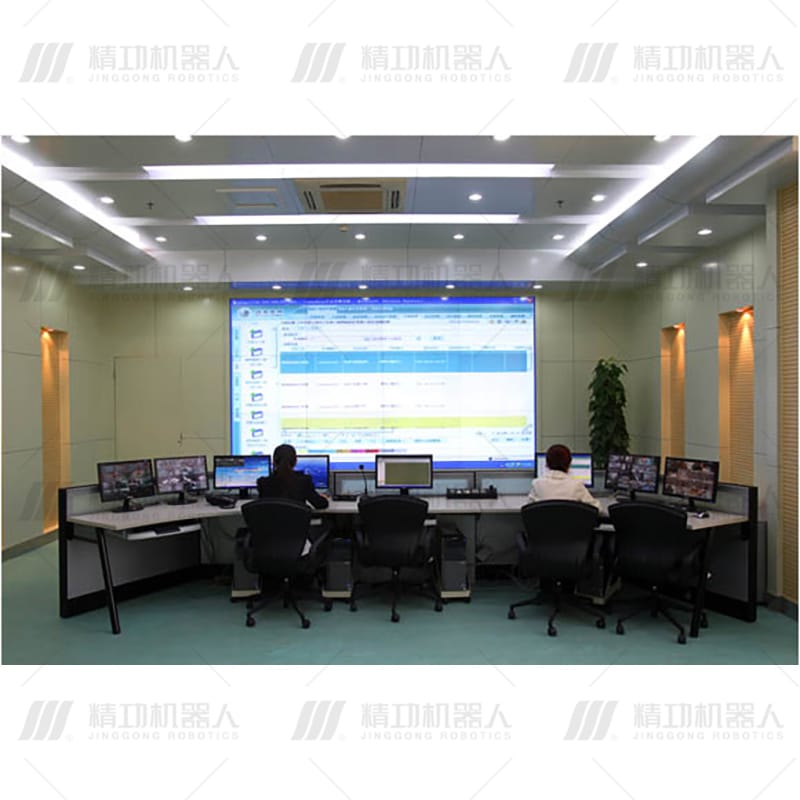
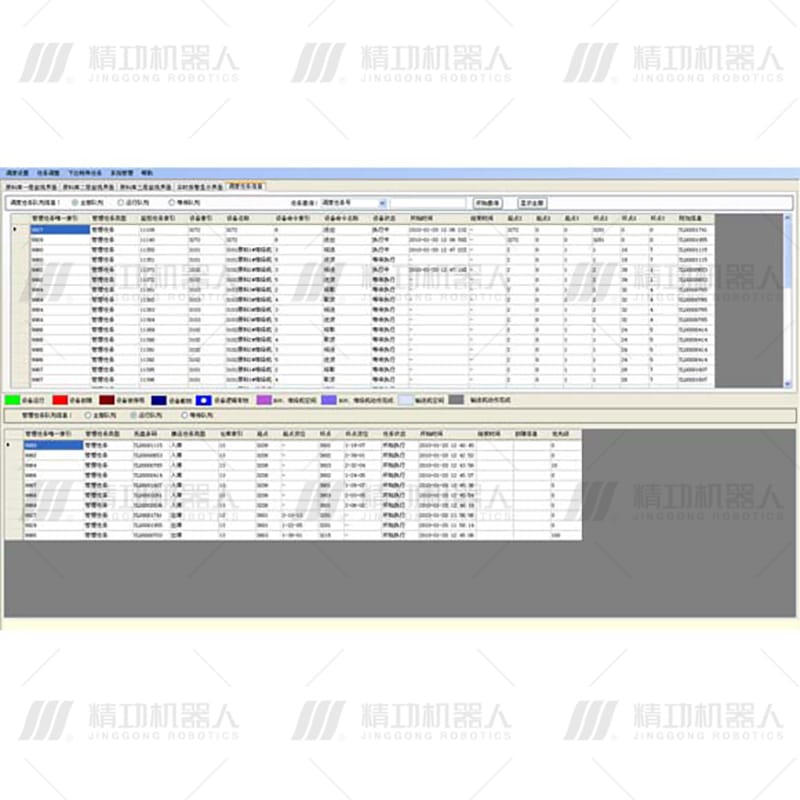
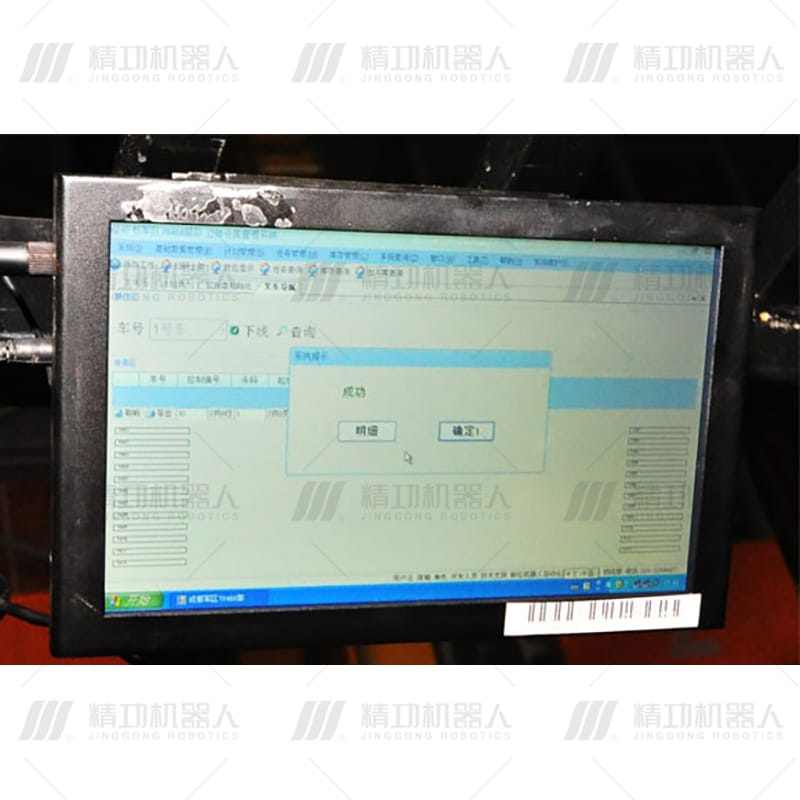